First Approach Adven's boiler, commissioned in 2023, experienced significant challenges related to...
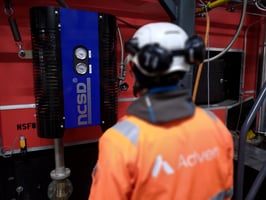
Slagging and fouling in steam boilers and HRSG disrupt efficiency, leading to unexpected shutdowns. Accumulated material is a common issue in many industries, causing filter clogs that damage equipment and increase air and electricity consumption.
Effective cleaning solutions are essential to maintain optimal operations and prevent costly disruptions.
Automatic operation
Cleaning without damaging
Economical solution
The NIRAFON system can be used in combination with existing cleaning system
Optimizing Boiler Performance: Comparative Test Runs at Suomenoja Power Plant (2000)
In the beginning of the year 2000, 18 sootblowers were utilized for boiler maintenance. However, during the summer outage, a strategic shift occurred. The traditional sootblowers were replaced with 12 advanced NIRAFON® 250-SS Acoustic Cleaners.
In the first graph, the reference points were selected to ensure comparable conditions. Specifically, the heat input to the boiler, measured in megawatts, remains consistent on days when the comparison values were recorded. The energy input into the boiler is uniform.
The second graph illustrates the thermal power obtained from the economizer, indicating how much heat energy is recovered from the flue gas into the water. In this case, the acoustic soot blower contributes more because the tubes, which the water and the flue gas flow through, are cleaner and facilitate better heat transfer from flue gas to water.
This graph depicts the pressure difference across the rotating air preheater. Generally, this is lower with an acoustic soot blower compared to a steam soot blower.
When the air preheater is cleaner the pressure does not rise with the air preheater, as the flow is more unobstructed, resulting in a smaller pressure differential before and after.
The graph outlines the daily steam consumption for soot blowing, which is naturally lower with acoustic soot blowing as it does not utilize steam whereas steam soot blowing does.
Since acoustic soot blowing is not in use throughout the entire boiler, steam consumption is not zero with acoustic soot blowing.